Process Filtration – Filter Housings
Process Filtration / Filter Housing Installation
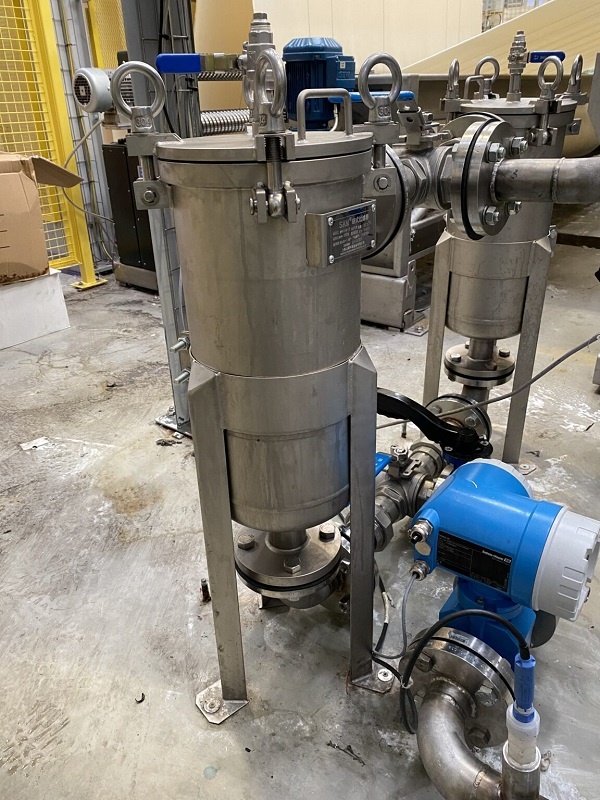
Process Filtration – Stainless Steel Filter Housing Project
An existing customer operates a fairly large process to scour (clean), a manufactured woven material. The material is produced on site on computer controlled looms.
The woven material is always impregnated with oil deposits which stem back to the production of the ‘beams’ (rolls of thread) by their supplier. Oil can also travel through the compressed air to the looms and be passed onto the material.
The material is cleaned before coating by the scouring line. The material is loaded on rolls and passes over a series of rollers to align the fabric and take out any major creases which stretches the fabric.
The objects produced that are in the work areas of the fabric rolls are perfectly finished, but the process leaves some loose nylon fibres at the edges of the rolls. As the fabric is stretched, nylon fibres are lost.
The fabric enters a wash bath which contains caustic soda to clean the fabric. The tank has a high pH around 12. As the fabric passes over multiple rollers in the first tank, fibres are lost to the water. As the fabric enters tank 2, the cleaning continues.
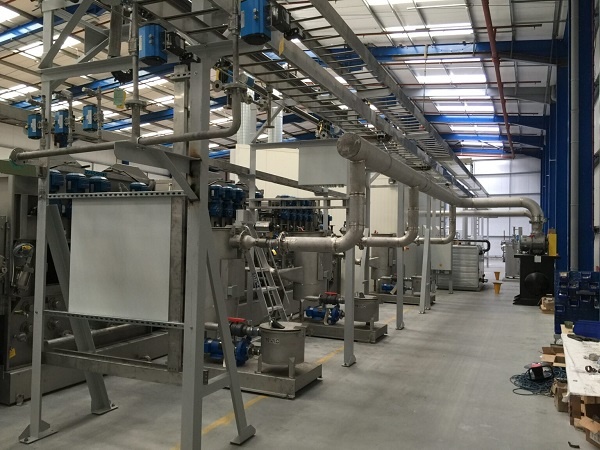
The original solution supplied with the machine contained a large stainless tank with a lid which gravity fed from the bottom of the first process tank. This contained a high and low level sensor, then supplied the suction side of a pump with a pH sensor in the suction line.
After a period of about two weeks, the tank and pump became blocked with nylon fibres, causing the pump to slow down and the pH on the plant to begin to drift heavily.
Although the pump was fed from an inverter, actually balancing the flow in and out of the external tank was problematic. The pump supplies tank 2, with a weir to allow the water back into tank 1 to complete the balancing process. Tank 2 regularly overflowed and pooled over the floor.
The site ran the machine for three years continually having down time and issues.
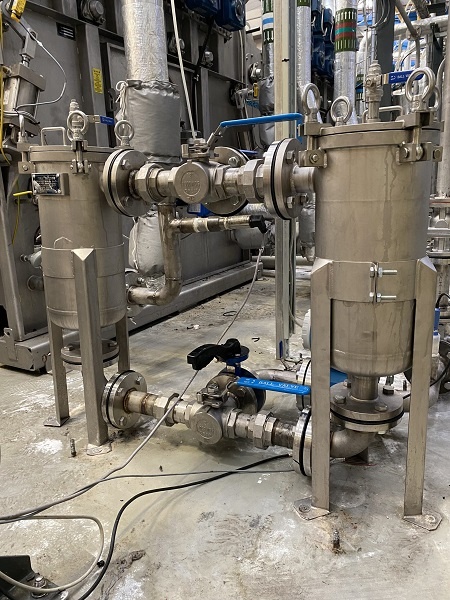
We proposed a solution and supplied a process filtration system using duplex stainless steel filter housings.
In order to maintain equilibrium within the system, we made it a closed system. The filter housings were carefully selected to make sure they were located just under the level of the water in the tank to avoid priming and air issues.
A single ball valve was installed at the tank for isolation then piped directly into the filter housing selector valve.
The water passes through a bag filter rated at 400 micron to remove the nylon fibres. The duplex feature enables a switch over mid operation to the second vessel without shutting down process on the machine.
As the water passes out of the filter housing, flow rate is monitored with an Endress Hauser flow meter before reaching the pump.
The flow meter is monitored by a PLC on the plant to display flow readings. An alarm is raised when the filter needs to be replaced, based on current flow rate.
The pump is now fully protected by the process filtration system and is no longer fouled with nylon fibres.
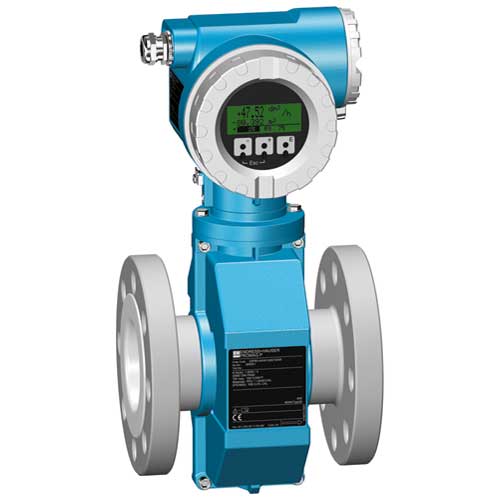
We moved the location of all the sensors to maintain throughput.
As the system is now a sealed loop, we no longer required a high level sensor. We designed the plant modification so it could not flood, even if the lids of the filter housings were left open.
The low level sensor for the pump protection was fitted back into the tank supply pipe, angled and located out of the flow. It was a basic fork sensor and only needed to be wet.
The pH sensor was located after the process filtration and flow meter. It no longer becomes contaminated with fibres as the water passes over it. Our Electrical Services engineer attended to modify the electrical systems on the line.
As the pump now runs on full power, the suction out of tank 1 enables the weir to work correctly from tank 2 and no longer over flows.
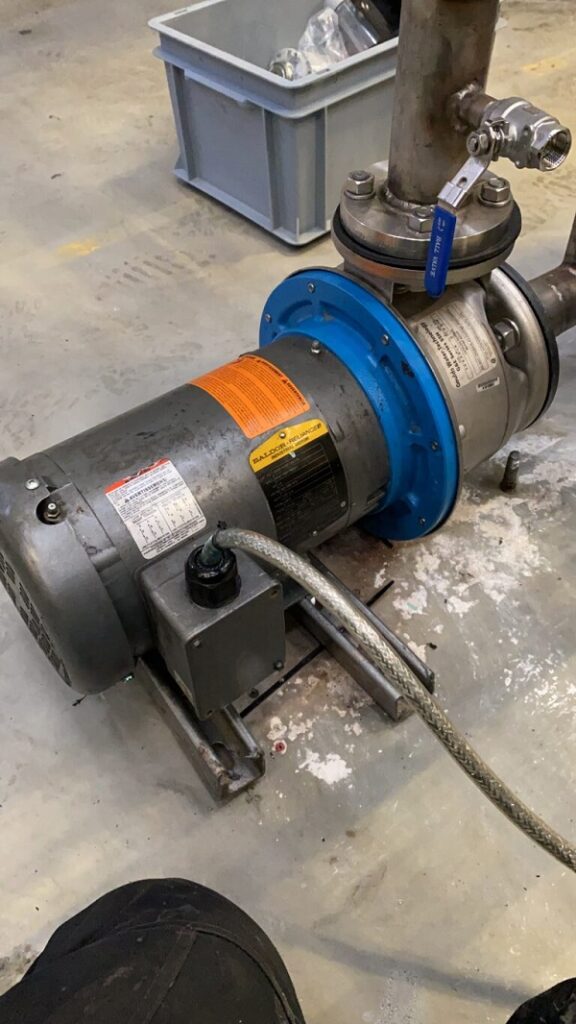
The end suction pump that came from the USA had a bad leak which we also fixed.
The pump was contaminated with nylon fibres which site maintenance regularly removed from the impellor.
We returned to the site during a recent week shut down and stripped the pump fully down. We found an O ring had failed between the impellor and shaft sleeve and the mechanical seal was passing.
The shaft seal was seized onto the shaft and took a few hours of work to remove it without causing any damage. Once this was off we could finally remove the mechanical seal and end housing.
Most of the shaft and sleeve were heavily corroded and we had to carefully remove the debris using wet and dry paper by hand, until they were polished and the parts would locate without using force.
Our stockist had an imperial seal kit on the shelf which we collected and returned to site the next day to fit.
The pump was re-assembled in reverse order and we carefully cleaned each of the components before assembling back onto the shaft.
The impellor was inspected and some rough edges were found probably caused by the nylon fibres. The edges were removed with a file by hand.
A new O ring was sourced and fitted between the impellor and shaft sleeve to prevent the issues from occurring again.
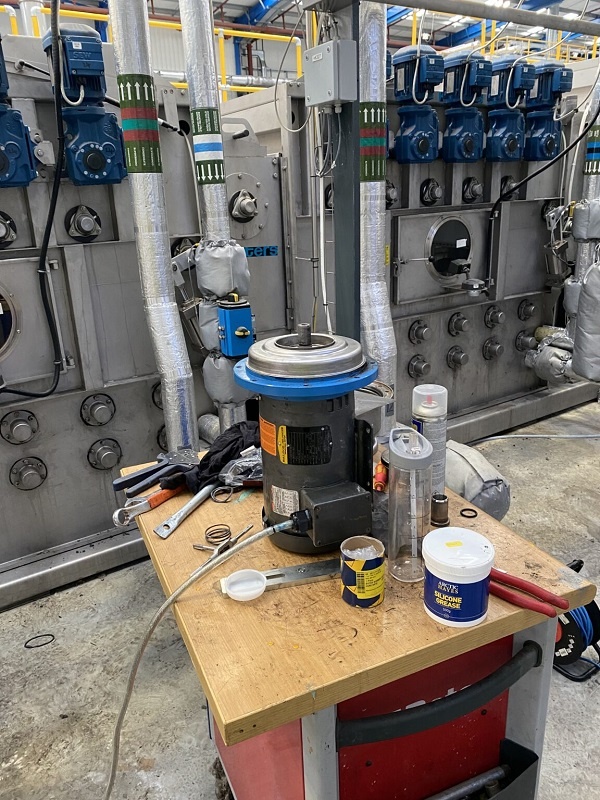
The main case O ring was replaced and gently coated in Silicone Grease before final re-assembly.
The impellor depth into the wear sleeve was checked before the pump was placed back into operation.
The entire system was then primed and tested.
When we left site the entire system was functioning well and the contamination was held back in the filter bags for easy dispoal.
As the scouring line is operated, the left over contamination in the tanks is gradually being removed at source.
Hamer Mechanical Services Ltd custom build process filtration systems with different types of filter housings. We also carry out Pipework Installation.
Feel free to contact us to discuss your existing system or to plan for a new modification.
Phil Hamer.