PLC Automation
PLC Automation goes hand in hand with the plant and equipment doing the work. Not only can it effortlessly control your plant, it can identify issues and show you an overall status live.
We work with Siemens S7-1200 based PLC systems. We have designed, built, installed and comissioned various plant, control systems and machine specific systems over many years.
Ideas, Think, Design
In order to contemplate designing a PLC automation control system, one must understand the mechanical equipment 150% before even putting pen to paper.
When we deisgn and build plant ourselves, integration of the control system starts with the initial plant concept and design, the two run hand in hand from start to finish.
For a retrofit idea, we need to spend time watching and learning how the existing equipment works. How it fails, how it goes wrong and how its users can affect or bypass its operation.
Once confident we can move onto build.
PLC Automation
Panel Build
Our panels start out life in the workshop. Component locations are marked, DIN rails are installed and comb trunking is fitted.
The chassis is then cleaned and the major components are installed.
Wire
Some PLC Automation panels can have hundreds of wires. Everything the machine does requires a multitude of controls:
- Digital Inputs
- Digital Outputs
- Analog Inputs
- Analog Outputs
Every single input and output is carefully routed from the control panel terminals to relays where required and back to the PLC.
Mains connections, circuit protection, filters etc are all wired and installed at this point.
Software Development
We get the actual assembled control panel fully inspected and tested, all conductors verified. The PLC Automation panel is then hooked up in our lab and powered up.
We connect to the system with TIA Portal and begin to write the software step by step.
We check and evaluate every step carefully checking for errors as we go.
We have tons of sensors, injectors and emulators in the lab which enables us to inject the panel with tons of signals for operation.
HMI Interface
Each item of the plant can be neatly presented on a touch screen display, taking real live information from the PLC Automation contol panel.
See your plant running in real time with real sensor figures. Warning pilot lights draw your attention directly to the problem. Identify issues easily so maintenance can be directed to the fault at hand.
Site Installation
When the site is ready for the PLC Automation control system, the panel can be shipped to site.
We can attend site and take care of the installation for you. If you select another contractor, we provide full drawings and a cheat sheet to simplify wiring by others.
Commissioning
During PLC Automation commissioning, we hook up TIA Portal on site and begin to bring the plant to life.
We operate the system from start to finish and make changes to the program live as we progress. Each step is vetified, fine tuned and made better if we can.
Once the system is accepted and handed over, we train the operators, staff and engineers who will maintain the system.
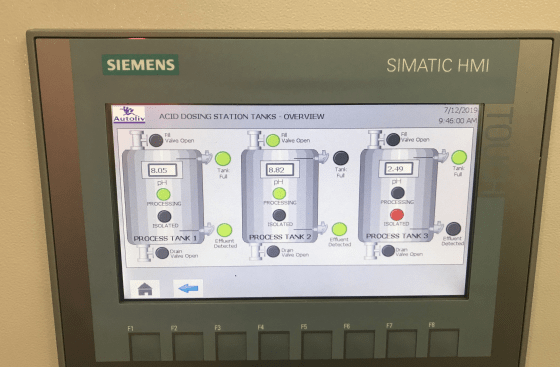
Scouring Line Acid Dosing Plant
Three large mixing tanks where acid is added to neutralise the pH with wash water from a scouring line.
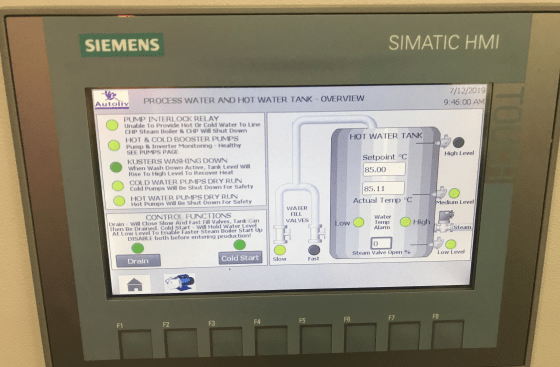
Hot Water Tank - Steam Heated
Process hot water tank (90 Deg ) heated with direct steam injectors. Various drain, startup and warning indicators.
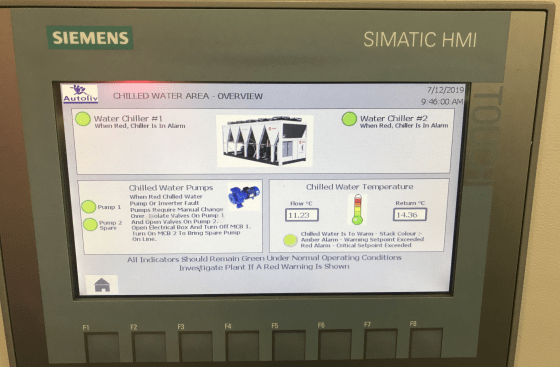
Water Chiller Screen
Page showing status of a water chiller, pump status and chilled water temperatures.