Modular Flooring – Plating Plant
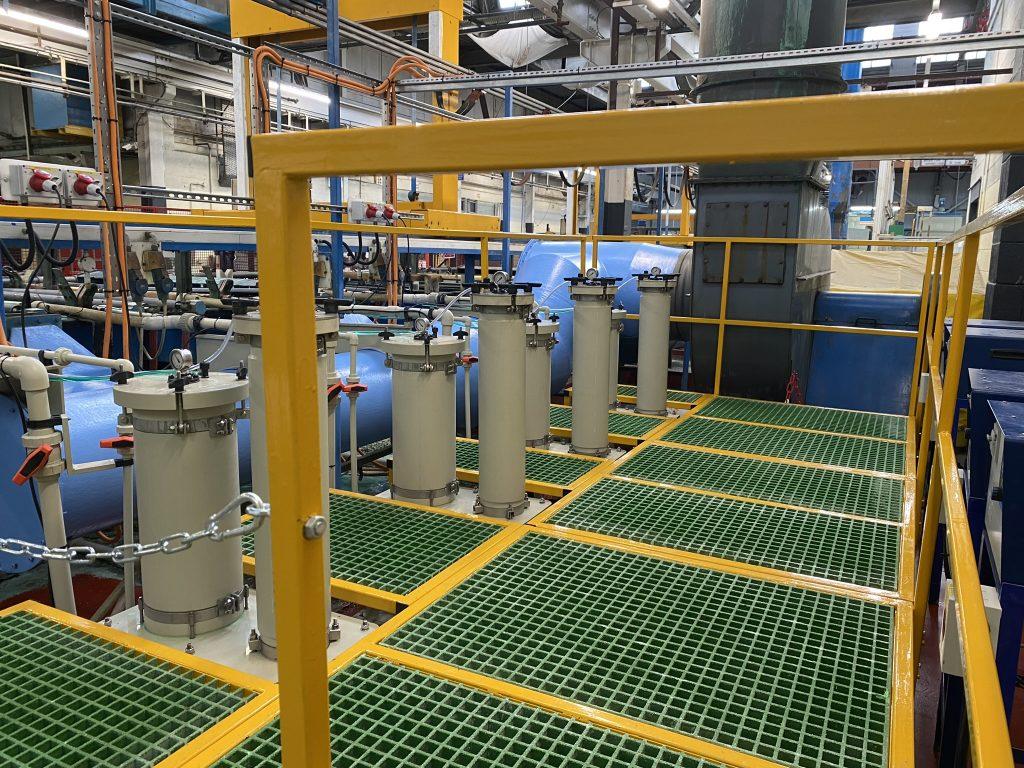
Modular Flooring system we designed, built and installed together with some pipework modifications working alongside the filter suppliers.
The customer had ordered three sets of replacement pump filters and arranged for these to be installed (by others). The height of the filters required a modular flooring system to be installed. The additional height of the modular flooring was required to enable the filter elements to be safely replaced.
The customer had already done some preliminary designs so we were able to offer a quote for the works fairly quickly.
We were instructed to design, build and supply the modular flooring system and to move the polypropylene pipe work feeding into the baths, to allow new larger bus bars to be added for the plating process.
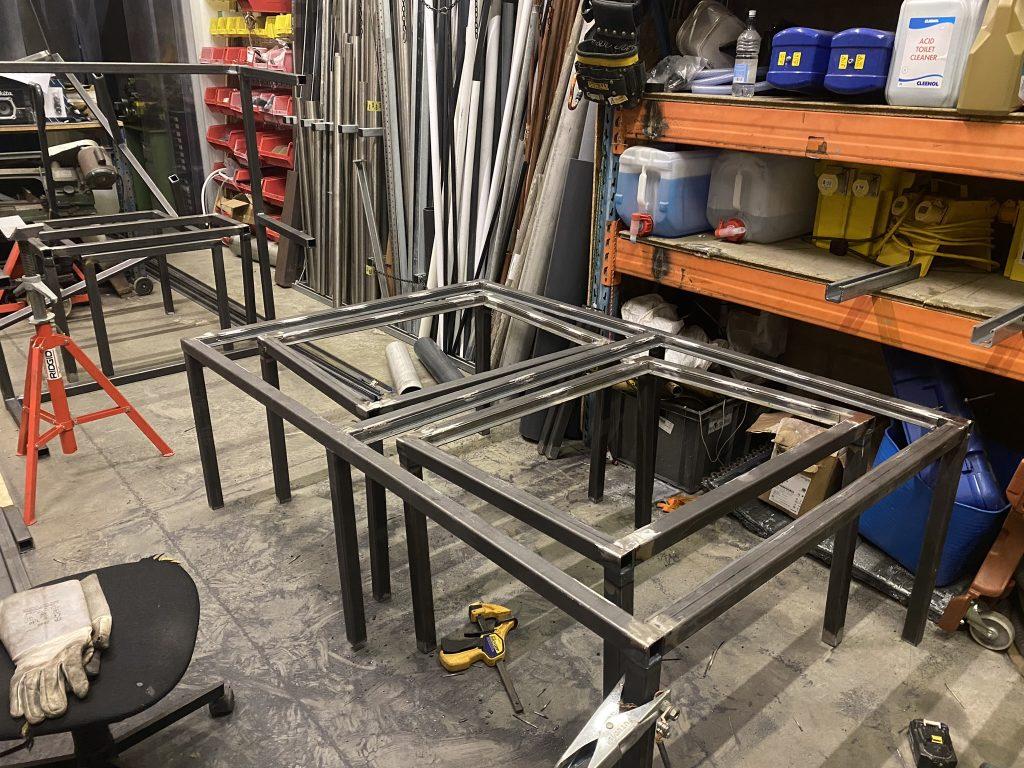
The modular flooring system was designed as nine modules. Each was a different size. Due to positioning over a bund, several of the legs were made with different lengths to compensate.
The modular flooring sections were all TIG welded in our workshop, sections cut from 7.5m lengths of box steel.
The modules were then measured to check for the fibreglass anti slip flooring to make sure the sizes were correct. This was then cut to size.
All of the welds were generally cleaned up and the surface fully wiped down and de-greased.
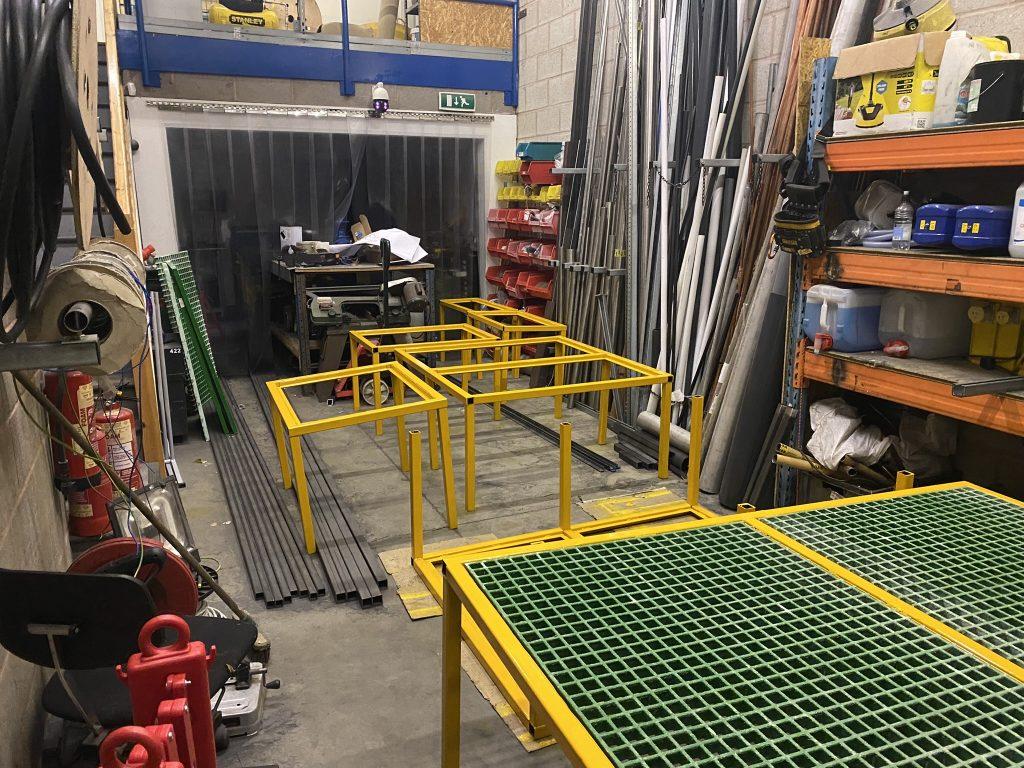
Each of the modules was then fully painted in the RAL colour specified by the client.
End caps were fitted into any open tube ends and the adjustable feet fitted.
The GRP Grid was then fitted into the modular flooring sections.
Four of the modules were configured with hinges to allow access below.
The modular flooring system was now ready for final assembly.
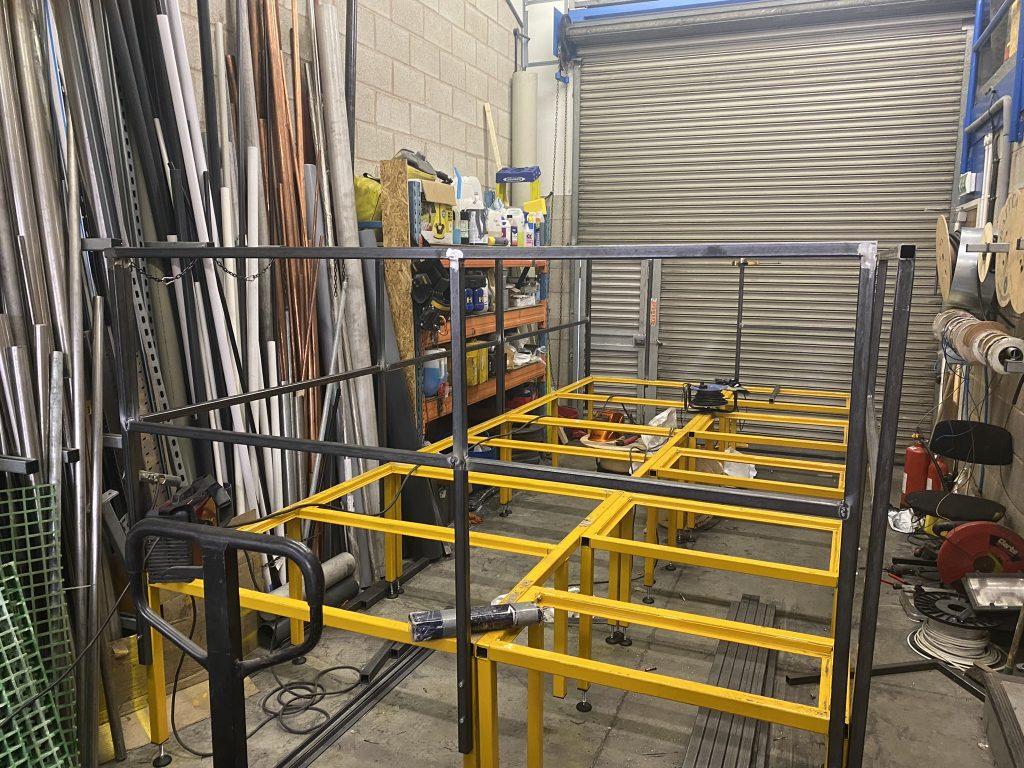
Each of the modules were laid out and carefully drilled to enable fixed assembly. Rivnuts were used throughout to add M8 threads as needed.
The vertical sections of the hand rails were all cut and fixed into place using the same method.
The remainder of the hand rail sections were cut and welded in position for best fit. Where required, the hand rails were joined.
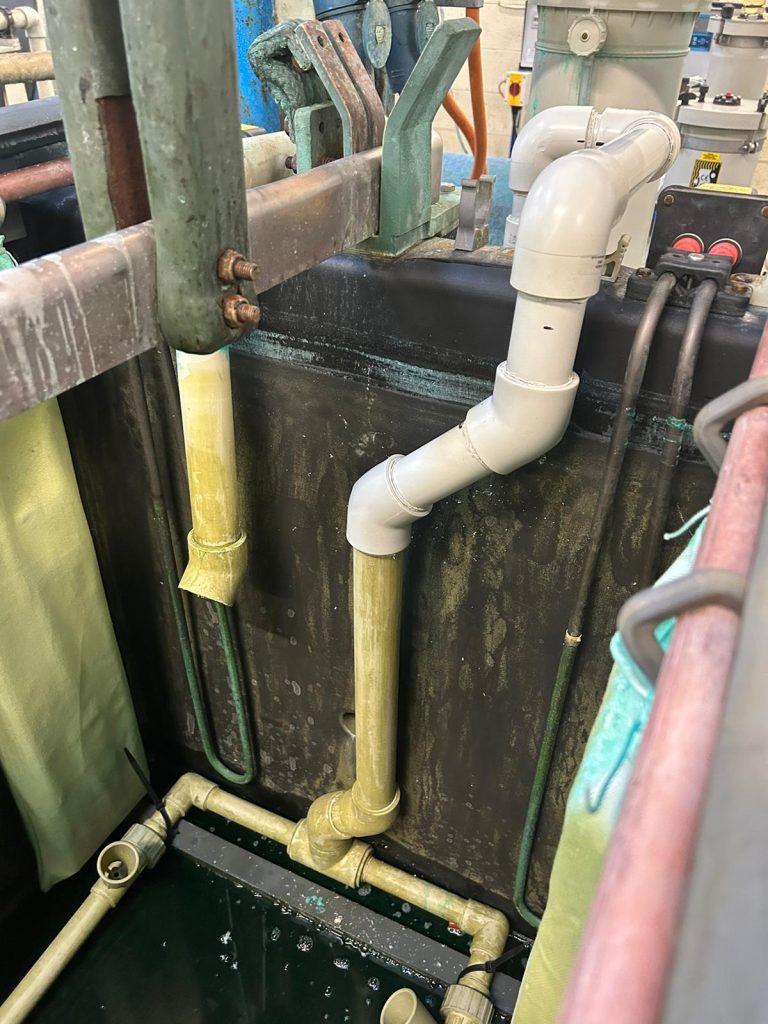
Before we delivered the modular flooring system to site, we had to prepare and modify some of the pipework.
The plating plant is having bigger copper bus bars installed. The existing recirculation pipe work would conflict with the DC modifications.
We attended site over four visits at 6:00 AM to modify each tank.
The old pipework was cut out and new polypropylene pipe work was socket welded into place.
One tank was done per visit so the plating plant could continue to operate as it has multiple tanks.
The existing pipe work was installed in 1.1/4″. As we modified each of the four legs, we socket welded a union into place.
This simplified the pipe work connections for the company who supplied and replaced the filters on site.
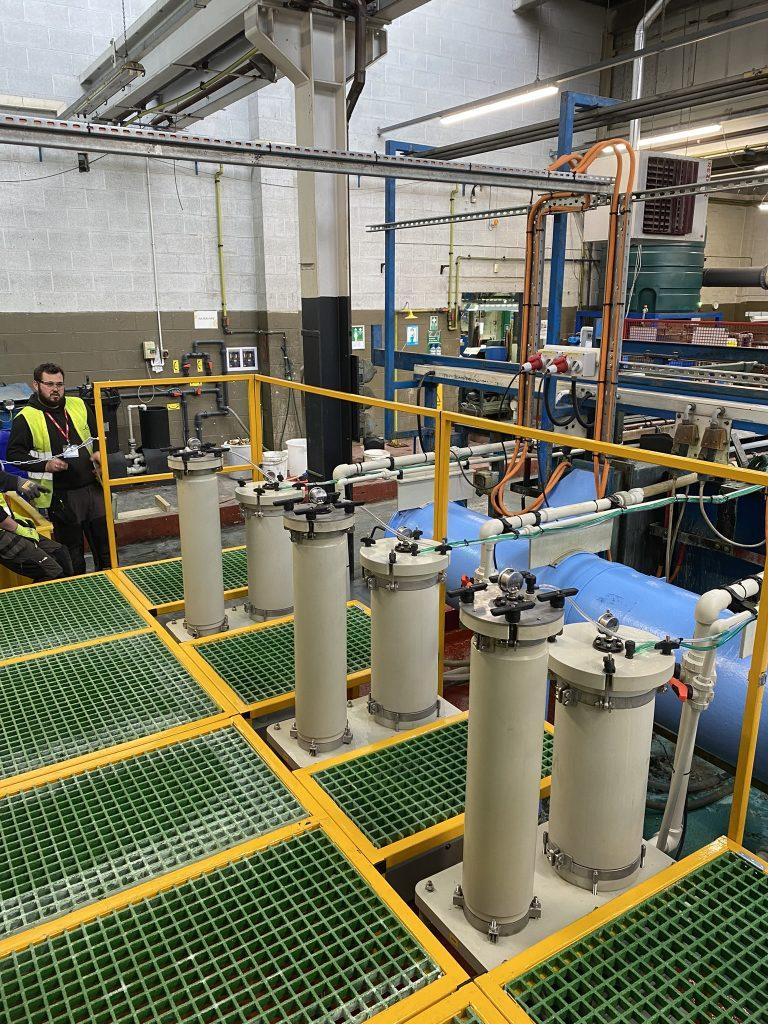
The filters, pumps and associated pipework were installed by a separate contractor.
We took all the sections of the flooring to site and successfully managed to get the modular flooring into position. It was a very tight squeeze.
It was bolted together and the hand rails bolted into place.
The GRP grid flooring was then installed and handed over to the customer.
Looking for a custom modular flooring project like this one? Please Contact Us.
See our pipework page by clicking here.
We specify George Fischer Polypropylene fittings.
Visit GF By Clicking Here.